
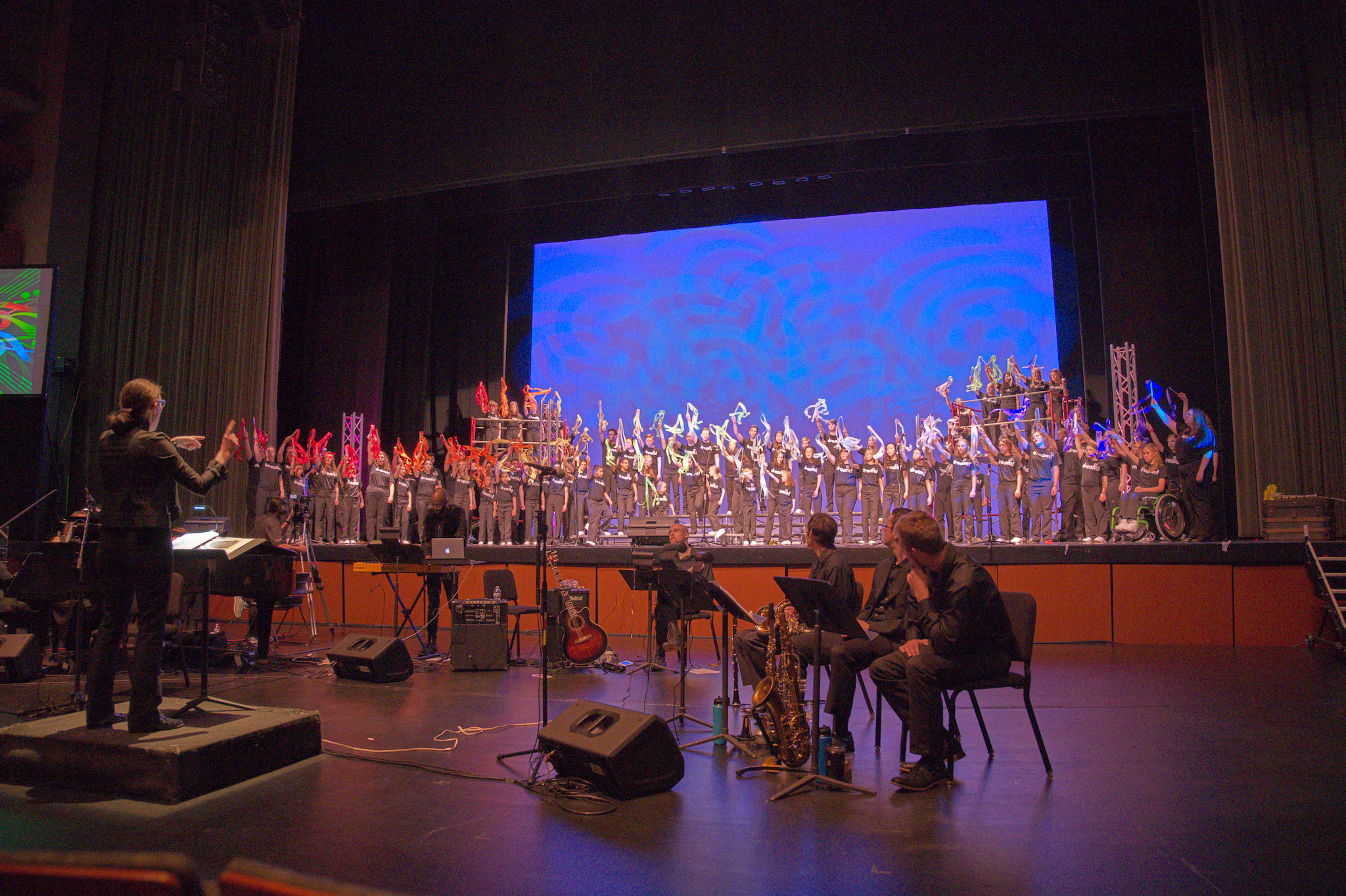
The alkoxybutenolide structure has an embedded acrylate functionality (depicted in pink in Fig.
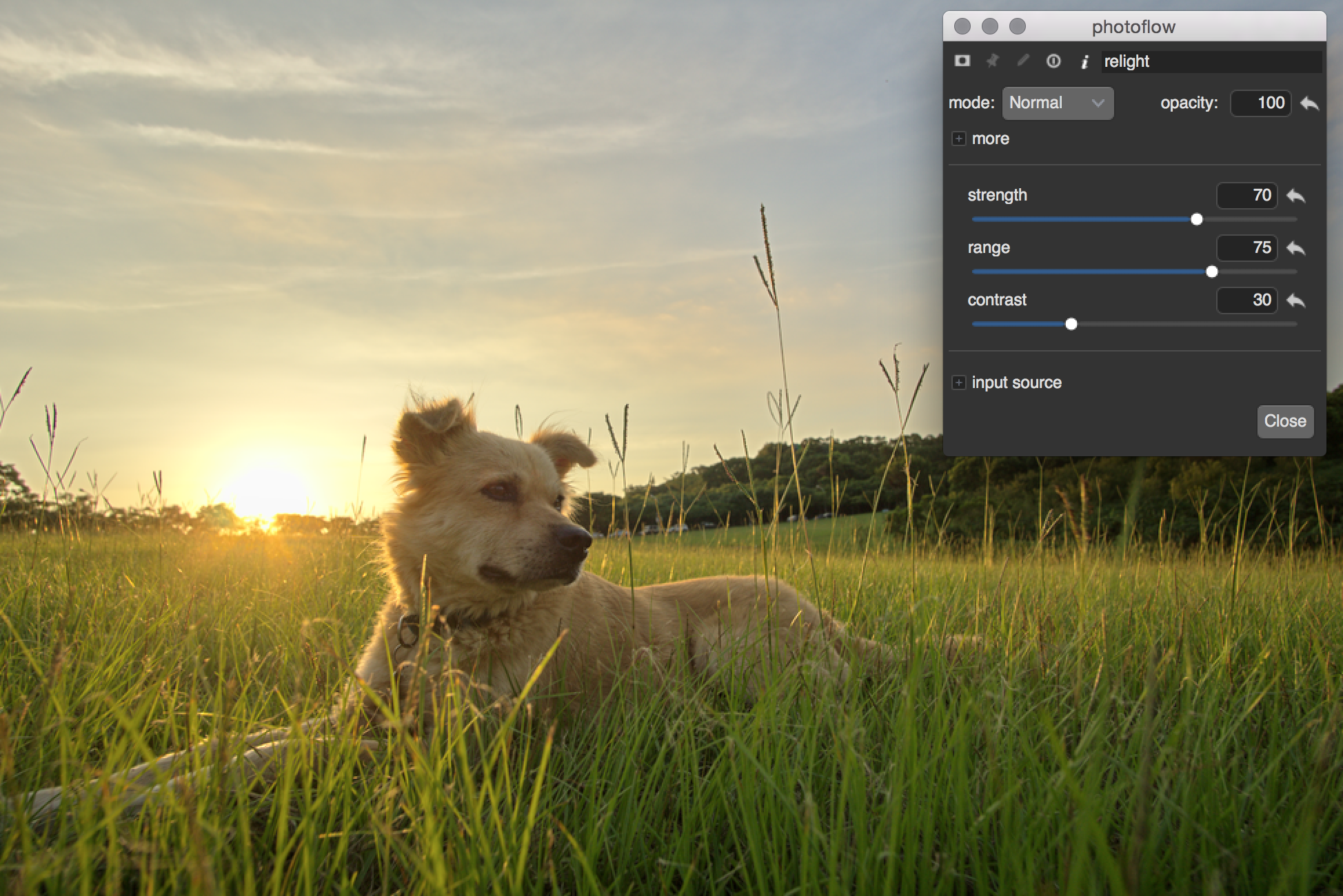
The furan moiety of furfural undergoes a cycloaddition with 1O 2 and transforms quantitatively into hydroxybutenolide, which can be readily converted into various alkoxybutenolides by heating with the appropriate alcohol ( Fig. This particularly clean process involves triplet-triplet annihilation of the excited photosensitizer and molecular oxygen. The next step is a photooxidation based on singlet oxygen ( 1O 2), which is generated using visible light and a catalytic triplet sensitizer. The starting point is biomass, e.g., lignocellulose, which is readily converted into valuable platform chemicals like furfural using acid-mediated dehydration ( Fig. 1A, implementing the Principles of Green Chemistry ( 26), we take an integrated approach using a renewable resource, green transformations, intrinsic functionality for polymerization, and tunable materials properties of the coatings. ( B) Photooxidation of the biomass-derived furfural followed by derivatization toward alkoxybutenolide monomers comprising an acrylate type structure (acrylate unit is shown in pink).
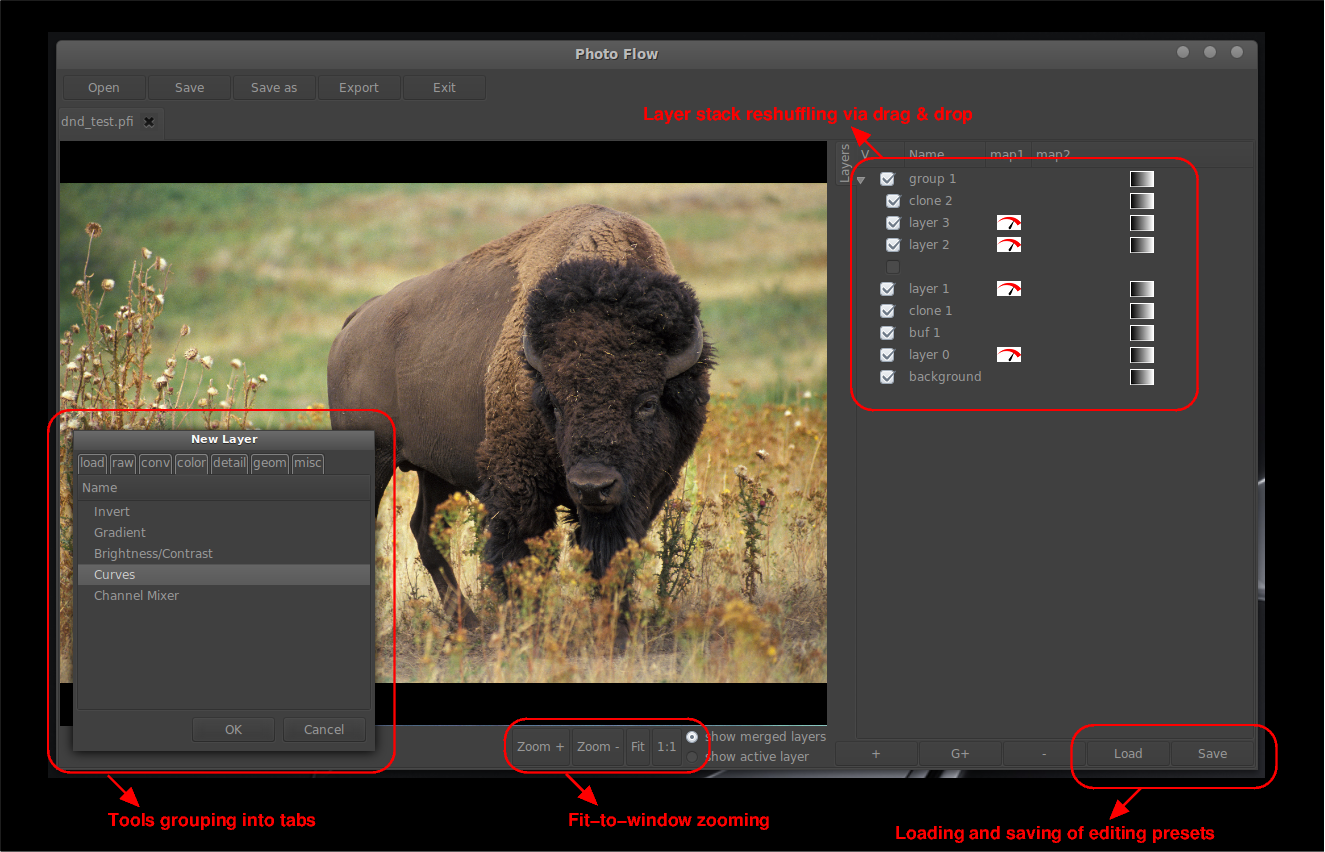
( A) General strategy for bio-based alternatives instead of common petrochemical-based acrylate monomers to yield coatings.
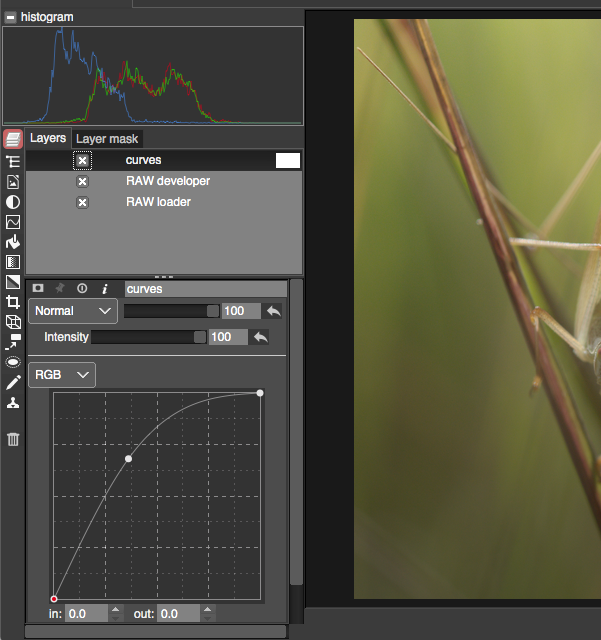
Here, we demonstrate the formation of high-performance coatings using lignocellulose-derived alkoxybutenolides as an alternative for acrylates while using a photooxidation process with visible light and oxygen in a scalable flow system to access the monomers.ĭesign of bio-based alternatives for acrylates and coatings. Although bio-based polyesters are now well established ( 9), limited reports on (co)polymerization of acrylate analogs did not reveal materials function ( 24) or indicated large differences in reactivity compared with common acrylates ( 25). Despite progress toward the use of renewable feedstock for fuels ( 8), polymers ( 9– 11), and specialty chemicals ( 12, 13), as well as recent advances in photoredox ( 14) and electrochemical conversions ( 15, 16) aiming at the design of benign and low waste transformations ( 17, 18), direct biomass-derived alternatives for acrylate-based coatings remain largely unexplored ( 18– 23). Global production of acrylate esters exceeds 3.5 million metric tons a year ( 7), and it is evident that sustainable alternatives, maintaining the favorable properties of acrylate-based materials, can be highly transformative in tomorrow’s chemistry and materials. In the multistep processes that are typically used nowadays, middle- to long-chain fossil-based hydrocarbons are converted into olefins via cracking, further oxidized and derivatized into acrylates, which are subsequently polymerized to yield a wide range of plastics, resins, and coatings ( Fig. However, the environmental awareness and the need to design the green chemistry of the future based on sustainable materials demand for renewable resources and waste-free, low-energy chemical conversions without compromising the function and performance of the final products ( 3– 5). The polymers and resins in coatings are manufactured using petrochemical feedstock ( 2). Coatings are omnipresent in daily life, indispensable in construction and applied to enhance properties and durability of numerous products, ranging from cans to cars ( 1).
